本文制备具有16个发光单元串联的HVLED芯片,采用光刻胶和SiO2双层掩膜使刻蚀后的隔离沟槽的侧壁平缓以便于电极连接,研究了隔离沟槽宽度对芯片电学性能和光学性能的影响。同时,使用商品化的镜面铝基板和陶瓷基板对HVLED进行封装,研究了注入电流、温度、基板对器件电学性能和光学性能的影响。
一、引言
高压发光二极管( HV-LED) 是在芯片制备过程中将一个大尺寸芯片划分为多个小发光单元,再将发光单元通过电极连接桥串联,从而实现的一种小电流、大电压的高功率LED。其发光效率可以通过优化发光单元的尺寸和形状,隔离沟槽宽度和侧壁微结构,以及制备背面反射镜等方式来提高。
台湾交通大学在芯片总尺寸不变的情况下制备了发光单元尺寸分别为370 μm × 221 μm和228 μm × 190 μm的HVLED芯片,结果表明: 单元尺寸较小的芯片,其电流扩展较均匀,发光效率较高。华南师范大学制备了发光单元横截面分别为矩形、倒梯形和正梯形的HV-LED芯片,结果表明:正梯形发光单元结构可使芯片获得较高的发光效率和制作良率。台湾中兴大学在隔离沟槽中填充聚合物实现沟槽的平坦化以便于电极连接,制备了隔离沟槽宽度分别为20、40、60、80 μm的HV-LED芯片,结果表明: 随着隔离沟槽宽度的增加,发光效率得以上升。本课题组在隔离沟槽的侧壁制备了柱状微结构,并优化了蓝宝石衬底下面的背部反射镜,提高了光提取效率从而增强了光输出。
HV-LED芯片的封装通常采用普通大功率LED芯片的COB(chip-on-board)封装形式。由于COB封装是直接将LED芯片粘贴在基板上,因此基板的导热性能和反射光性能就尤为重要。陶瓷基板具有较好的耐腐性和较高的热导率( 约24 W/(m·K) ) ,且与芯片蓝宝石衬底的热膨胀系数( 约7×10-6 mm/℃) 相一致,因此封装后的稳定性较高,较好地解决了LED的散热问题和寿命问题;而镜面铝基板则具有更高的热导率( 约137 W/(m·K) ) 和反射率( 约98% ) ,能够有效地提高大功率LED芯片的饱和输出功率。
二、HV-LED芯片
1.芯片制备
实验使用的5.08 cm(2 in)外延片是采用图形化蓝宝石衬底(PSS)通过金属有机化学气相沉积(MOCVD)获得的。外延片结构从下至上分别是:0.025μm缓冲层、3.5μm未掺杂的GaN层、2.7μm掺硅的n-GaN、0.24μm多量子阱有源区、0.25μm掺镁的p-GaN。制备完成的高压LED芯片由16个发光单元串联构成,如图1所示。发光单元的排列形式为[3,5,5,3],第一列和最后一列的单元数为3,第二列和第三列的单元数为5,各单元的尺寸相互匹配使芯片呈矩形,以便于后续的激光切割工艺。
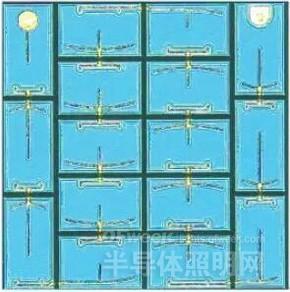
图1 HV-LED芯片的金相显微镜照片
具体的制备工艺如图2所示。首先,采用光刻胶作掩膜、Cl2和BCl3为刻蚀气体,使用感应耦合等离子(ICP)刻蚀出1.2μm的台阶,暴露出n-GaN层。接着,采用光刻胶和SiO2双层掩膜,使用ICP刻蚀直至蓝宝石衬底形成隔离沟槽,以实现各发光单元之间的电学隔离。然后,使用电子束蒸发在p-GaN上沉积100nm的ITO薄膜作为电流扩展层,再使用等离子增强化学气相沉积(PECVD)制备700 nm厚的SiO2钝化层,该层还使隔离沟槽的侧壁绝缘以防止漏电。最后,使用HF溶液湿法腐蚀将n电极和p电极位置暴露,通过电子束蒸发沉积50 nm/50 nm/1200 nm的Cr/Pt/Au金属电极将发光单元串联。在上述工艺基础上,经过后续的研磨、抛光、背镀、切割及崩裂工艺,制备出单颗的HV-LED芯片。
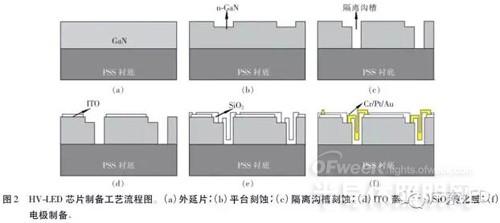
采用上述工艺制备隔离沟槽宽度分别为10、20、30、40 μm的高压LED芯片。为使芯片的形状保持为矩形,4种样品的第二列和第三列发光单元尺寸保持不变,而第一列和第五列发光单元的长度需略做调整。此外,在刻蚀隔离沟槽时,采用侧面微结构技术,发光单元的隔离沟槽侧壁如图3所示。
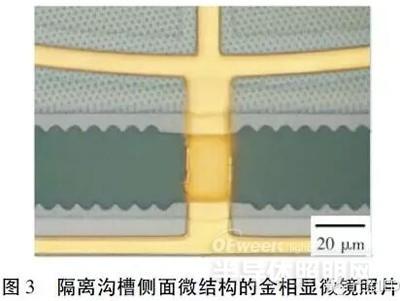
2.芯片测试与结果分析
采用配有半积分球的全自动晶圆点测机(型号LEDA-8F P7202)对4种样品的光学参数和电学参数进行测试,每种样品测试的芯片数量均超过200颗,注入电流范围为10~50 mA,典型电流-电压曲线、电流-光功率和电流-电光转换效率曲线如图4所示。随着注入电流的增大,正向电压和输出光功率均逐渐增大,而电光转换效率则逐渐减小。4种样品的变化趋势相类似,隔离沟槽宽度为20μm的芯片具有较低的正向电压和较高的输出光功率及电光转换效率。其中,正向电压在注入电流较大时出现饱和,特别是隔离沟槽宽度为40μm的芯片样品的饱和电流最小,这可能是因为隔离沟槽宽度为40μm的芯片样品的总电阻最大,芯片产生较多的热而使得少数载流子浓度较高,反向饱和电流较大,从而导致正向电压降低。
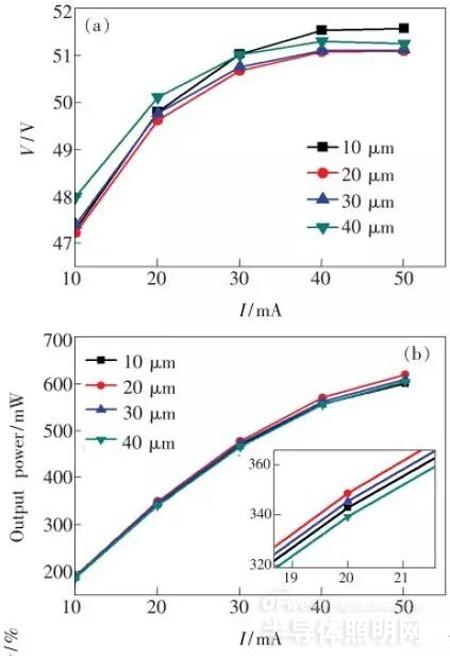
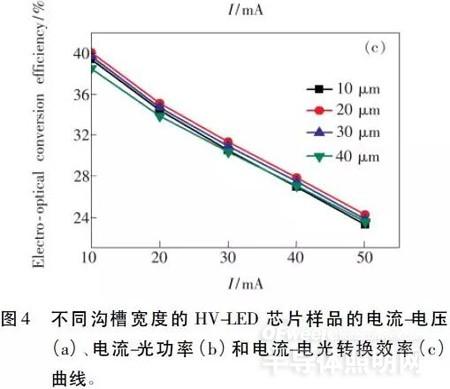
当注入电流为20 mA时,测试结果的平均值如表1所示。随着隔离沟槽宽度从10μm增加至40μm,HV-LED芯片的正向电压先减小后增大,在隔离沟槽宽度为20μm时为最小值50.72V。输出光功率先增大后减小,在隔离沟槽宽度为20μm时为最大值373.64 mW。这使得电光转换效率也先增大后减小,在隔离沟槽宽度为20μm时为最大值36.83%。正向电压呈现先降后升的趋势,是由于隔离沟槽处电极连接桥的电阻不同所导致的。当隔离沟槽宽度为10μm时,金属蒸镀质量较差,电阻率较高,使得电极连接桥的电阻较高,所以芯片的电压较大;当隔离沟槽宽度增大至20μm时,金属蒸镀质量较好,电阻率较低,使得电极连接桥的电阻减小,芯片的电压下降;随着隔离沟槽宽度的进一步变大,电极连接桥的电阻随着长度的增加而增大,使得芯片的电压升高。输出光功率呈现先升后降的趋势,这是由于相邻发光单元的光耦合能力不同。当隔离沟槽宽度为10μm时,从某一发光单元侧壁射出的光将较多地耦合进相邻的发光单元,由于发光单元内GaN材料、金属电极、量子阱等处的吸收,使得光提取效率较小,所以出射的光功率较低;当隔离沟槽宽度为20μm时,从发光单元侧壁出射的光将较少地耦合进相邻的发光单元,使得光提取效率增大,所以出射的光功率提高;随着隔离沟槽宽度的进一步增大,出射的光功率有所下降,其原因可能是由于总电阻变大使得芯片产生较多的热而导致内量子效率下降。
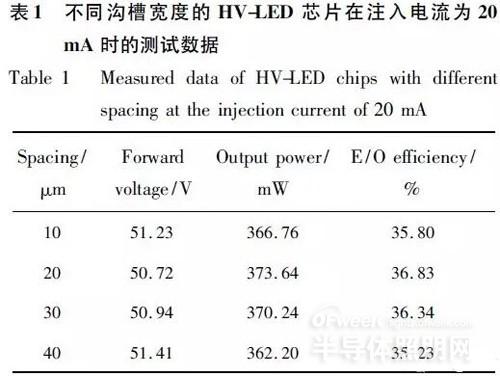
在上述实验中,对于隔离沟槽宽度为10、20、30、40μm的几种情况,输出光功率和电光转换效率的最大值出现在宽度为20μm处,这与上述文献的结果不同,上述文献在隔离沟槽中填充聚合物以实现沟槽的平坦化以便于电极连接。当隔离沟槽的宽度较小时,聚合物内部将出现孔洞,降低光提取效率,从而使得输出光功率和电光转化效率下降。当隔离沟槽宽度为20、40、60、80μm时,随着沟槽宽度的增加,聚合物的填充质量变优,孔洞减少,光提取效率增加,输出光功率和电光转换效率上升,即沟槽宽度在最大值80μm处最优。而本文采用光刻胶和SiO2双层掩膜,使得ICP刻蚀后的隔离沟槽的侧壁坡度平缓化以便于电极连接。此时,隔离沟槽之间是空气,影响光提取效率的主要因素不再是隔离沟槽之间聚合物内部的孔洞,而是相邻发光单元之间的光耦合能力。
三、4颗芯片封装的HV-LED器件
1.器件封装
选取隔离沟槽宽度为20μm的芯片样品进行封装。为获得接近市电的220 V,将4颗芯片样品串联。图5和图6分别是采用镜面铝基板和陶瓷基板封装的显微镜照片,4颗芯片呈“一”字形排列。具体封装工艺流程如下:首先,采用绝缘胶将HV-LED芯片固定在封装基板上,在150℃下烘烤2 h固晶;然后,使用焊线机进行金线焊接,4个HV-LED芯片串联,第一个芯片的p电极、第4个芯片的n电极分别与基板正、负极相连;再使用围坝胶圈定适合的点胶范围,为便于比较测试结果,镜面铝基板和陶瓷基板封装样品的围坝范围相同,直径均为10 mm;最后,根据6000 K色温要求将适量的封装胶(A胶/B胶)和荧光粉(黄粉/红粉)搅拌均匀,点入围坝范围内。
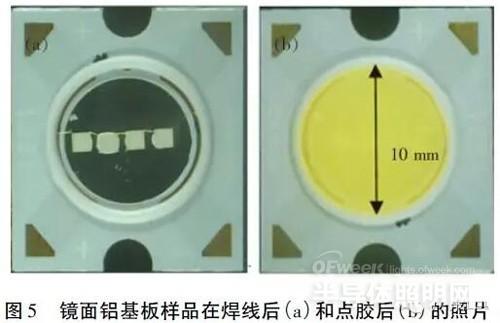
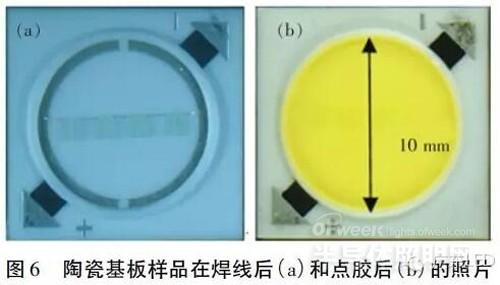
2.器件测试与结果分析
采用半自动分光分色测试系统(ZWL-3900)对样品的光学参数和电学参数进行测试,每种样品测试的器件数量均超过5颗,注入电流范围为10~100 mA,测试系统加热基板的温度为20、120、150 ℃。典型的电流-电压、电流-光功率和发光效率曲线如图7所示。随着注入电流的增大,正向电压逐渐增大,输出光功率先增大后减小,出现明显的光衰(efficiency droop)效应,发光效率下降。这说明4颗芯片封装的HV-LED器件仅适合小电流密度的情况。随着基板温度的升高,正向电压、输出光功率、饱和光功率、饱和电流和发光效率都呈下降趋势,这是由于温度升高使得芯片的少数载流子浓度增大、内量子效率和荧光粉的量子效率下降。在相同基板温度、相同注入电流的情况下,镜面铝基板样品的输出光功率、饱和光功率、饱和电流和发光效率都要优于陶瓷基板的测试结果,且镜面铝基板样品在达到饱和功率后,随着注入电流的增加,其输出光功率的衰减较慢。这是因为镜面铝基板的热导率和反射率都要高于陶瓷基板。另外,在相同基板温度、相同注入电流的情况下,镜面铝基板样品的正向电压较高。这是因为实验中使用的镜面铝基板LED支架的电路金属材料为铜,而陶瓷基板LED支架的电路金属材料为银。一方面,金属铜的电阻率比金属银的低;另一方面,金属铜暴露在空气中容易生成高电阻性的氧化铜,在金线焊接时形成的接触电阻较大,而金属银的氧化物是一种良导体,在金线焊接时形成的接触电阻较小。
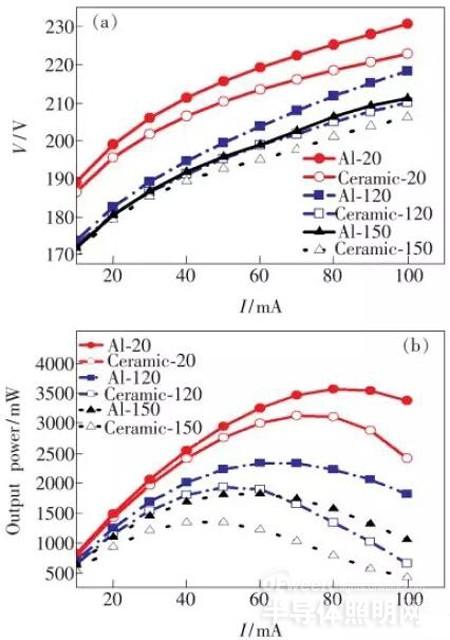
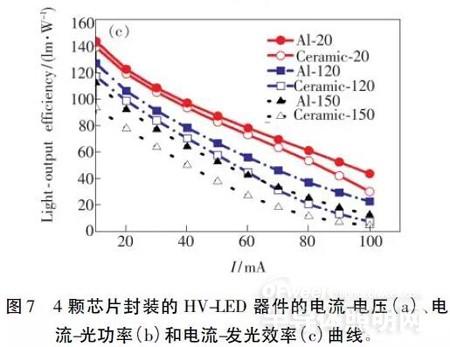
当注入电流为20 mA时,镜面铝基板和陶瓷基板封装的HV-LED器件的测试数据如表2所示。常温下,陶瓷基板封装样品的正向电压是195.4 V,发光效率是118.8 lm/W;镜面铝基板封装样品的正向电压是198.9 V,发光效率为122.2 lm/W。与采用陶瓷基板封装的HV-LED器件相比,镜面铝基板封装器件的发光效率更高。但是,陶瓷基板与LED芯片蓝宝石衬底的热膨胀系数相近,在自动化封装工艺中不会因高温而产生芯片歪斜的问题,而且陶瓷基板的绝缘性好、耐压高,所以在大功率倒装LED芯片封装中的应用越来越广泛。
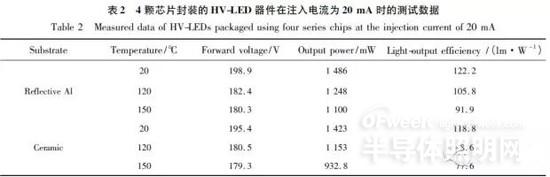
在不同的注入电流和基板温度下,典型的光谱如图8所示,峰值波长如表3所示。注入电流为20 mA且基板温度为20℃时,镜面铝基板和陶瓷基板封装的HV-LED器件具有相同的蓝光峰值波长457 nm。随着注入电流的增大和基板温度的上升,蓝光峰值波长出现红移,这是因为注入电流增大和基板温度上升都使得芯片结温上升,量子阱带隙下降。由于镜面铝基板的热导率要高于陶瓷基板,所以采用镜面铝基板封装的HV-LED器件的蓝光峰值波长红移较小。
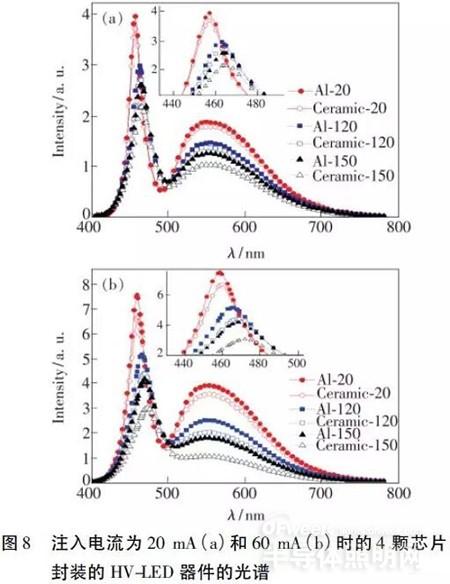
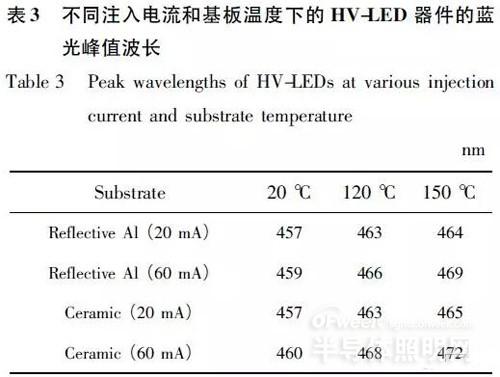
四、结论
制备了隔离沟槽宽度分别为10、20、30、40μm的高压LED芯片。当沟槽宽度为20μm时,芯片的电压较低,输出光功率较高,电光转换效率最优;当注入电流为20 mA时,芯片的正向电压为50.72 V,输出光功率为373.64 mW,电光转换效率为36.83%。
采用镜面铝基板和陶瓷基板进行4颗芯片串联形式的COB封装。由于镜面铝基板的热导率和反射率高于陶瓷基板,所以其封装样品的输出光功率、饱和光功率、饱和电流、发光效率、光衰及温度造成的蓝光峰值波长红移均优于陶瓷基板的测试结果。当注入电流为20 mA且基板温度为20 ℃时,镜面铝基板封装的HV-LED器件的正向电压是198.9 V,发光效率为122.2 lm/W。
LED器件的发光效率可以通过使用高效率的外延片、开发高光提取效率的芯片工艺、涂覆高效率的荧光粉、优选镜面铝基板LED支架的电路金属材料等方法进一步提升。