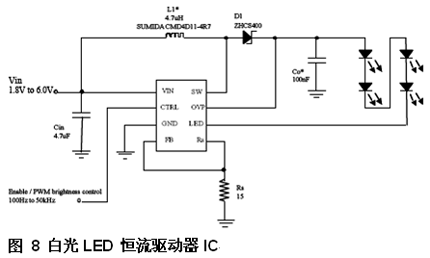
电流感应电压被降至250mV,且过压保护功能被集成到一个采用小型3mm×3mmQFN封装的器件中。其效率曲线如图9和图10所示。
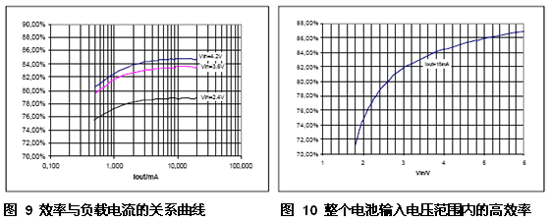
图10显示整个锂离子电池电压范围(2.7V~4.2V)内均可以实现80%以上的效率。在此应用中,使用了一个高度仅为1.2mm的电感(Sumida CMD4D11-4R7,3.5mm*5.3mm*1.2mm)。
从图10中的效率曲线可以看出:在大多数应用中,升压转换器可以实现比充电泵解决方案更高的效率。但是,在无线应用中使用升压转换器或充电泵时还需要考虑EMI问题。
对EMI加以控制
由于这两款解决方案均为运行在高达1MHz转换频率上的开关转换器,且可以快速的上升和下降,因此无论使用哪一种解决方案(充电泵还是升压转换器)都必须要特别谨慎。如果使用的是充电泵解决方案,则不需要使用电感,因此也就不存在磁场会引起EMI的问题了。但是,充电泵解决方案的飞跨电容通过在高频率时开启和关闭开关来持续地充电和放电。这将引起电流峰值和极快的上升,并对其他电路发生干扰。因此飞跨电容应该尽可能地靠近IC连接,且线迹要非常短以最小化EMI放射。必须使用一个低ESR输入电容以最小化高电流峰值(尤其是出现在输入端的电流峰值)。
如果使用的是一款升压转换器,则屏蔽电感器将拥有一个更为有限的磁场,从而实现更好的EMI性能。应对转换器的转换频率加以选择以最小化所有对该系统无线部分产生的干扰。PCB布局将对EMI产生重大影响,尤其要将承载开关或AC电流的线迹保持尽可能小以最小化EMI放射,如图11所示。
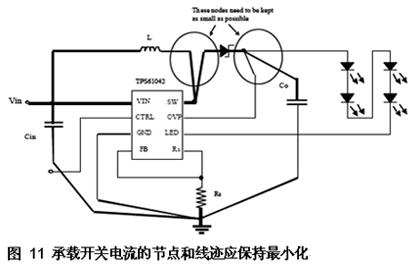
粗线迹应先完成布线,且必须使用一个星形接地或接地层以最小化噪声。输入和输出电容应为低ESR陶瓷电容以最小化输入和输出电压纹波。
结论
在大多数应用中,与充电泵相比,升压转换器显示出了更高的效率。使用一个升压转换器(其电感大小与1210外壳尺寸一样)降低了充电泵在总体解决方案尺寸方面的优势。至少需要根据总体解决方案的尺寸对效率进行评估。在EMI性能方面,对升压转换器的设计还需要考虑更多因素和对更多相关知识的了解。
总之,对于许多系统而言,尤其在器件拥有一个从1.0到1.5的灵活转换增益的时候,充电泵解决方案将是一个不错的解决方案。在稍微高于LED正向电压处发生从1.0到1.5的转换增益时,这样一款解决方案将实现绝佳的效率。在为每个应用选择升压转换器或充电泵解决方案时,需要充分考虑便携式系统的关键要求。如果效率是关键的要求,则升压转换器将为更适宜的解决方案。